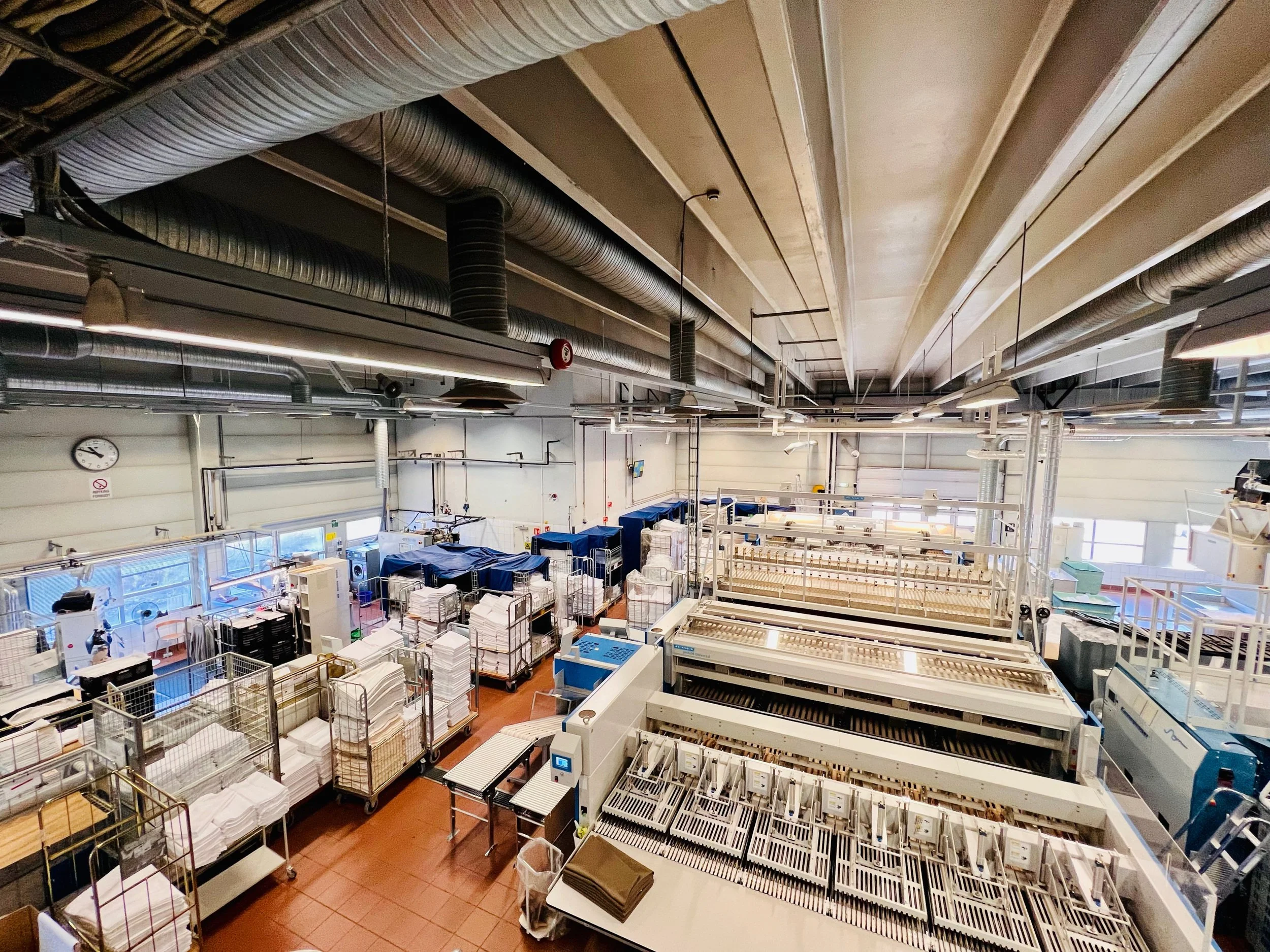
CASE STUDY
Laundry Efficiency Redefined
How to save costs by wash water reuse and then reap extra benefits?
Read how recycling at Nor Tekstil’s Vidar Vask plant exceeded all expectations.
Nor Tekstil’s Story at Vidar Vask
Founded some 50 years ago and part of the Nor Tekstil laundry group for approximately the last 10 years, the Vidar Vask laundry is located in Oslo, Norway’s lovely capital city.
At the Vidar Vask location, Nor Tekstil washes mostly for restaurants, including a number of Michelin star establishments. Vidar Vask’s big expertise is in laundering of fine table linen. With washing volumes of around 10 tonnes/week, Vidar Vask makes use of 6 washer extractors and also has a small dry cleaning section.
Positive results from Wientjens water and energy recycling equipment in other Nor Tekstil laundries had brought a good understanding of what Wientjens equipment can achieve.
P
High water costs and availability worries
Although the general impression abroad might be that Norway has plentiful fresh water, in fact fresh water availability has become a big issue, particularly in Oslo. A major infrastructural project to tackle this issue, the New Water Supply Oslo Project, was started in 2022 and is due to complete only in 2028. Water prices in Oslo have already risen steeply and the mayor has warned to expect up to 60% further price rises. Water costs in Norway are typically variable and can be very high, a breathtaking €65,-/m3 was even recently recorded in Oslo for a period.
Nor Tekstil laundry group takes water as a resource very seriously and their Vidar Vask laundry plant was already looking to cut fresh water usage (and costs) as well as to optimise its wash process even before the water shortages really hit. The timing of this project was prescient.
The Solution
In collaboration with Jako, specialist laundry advisors and suppliers, and Wientjens local partner in Norway, Nor Tekstil considered a number of options to reduce laundry water usage. Important input was also given by Nor Tekstil’s detergent supplier.
Recycling wash water immediately presented as the number one choice to make significant water savings in Vidar Vask. In order to enable use of recycled wash water while maintaining process flexibility, Jako proposed installing a Wientjens Blue Ocean Filter. With a capacity of 15m3/hour, a Blue Ocean Filter had more than enough capacity for Vidar Vasks’s washer extractors.
With fluctuating demand in the wash process, and with a summer demand peak, Vidar Vask needed significant flexibility to be built into the recycling process by way of buffers.
In one compact unit, the Blue Ocean Filter offered Vidar Vask not only generous recycling capacity but also a filtrate buffer of 1800 litres, more than sufficient to manage fluctuations in laundry process demand. Nor Teksil knew from experience that the Blue Ocean Filter is both straightforward to install, and easy to run, as well as allowing tailoring of its settings to the local laundry’s needs.
A Wientjens AquaDrain, to filter backflush water, was also included in the project, a small extra investment but one which greatly improves quality of laundry discharge water, a concern too for Nor Tekstil, as sewage disposal costs are on the rise.
The most important factor in the investment decision as far as Nor Tekstil was concerned was water savings potential. Jako calculated a possible reduction of water usage for Vidar Vask of 33%, with further energy savings too, leading to an estimated ROI of around 3 years. The deal was sealed.
Results
The sales order was signed by mid May 2022, by October the same year the Blue Ocean Filter was up and running in Oslo. Installation and commissioning of the unit by Jako was straightforward. Then began further process optimisation by Nor Tekstil engineers together with Jako, taking a few weeks more. During all this time, the laundry ran without any disruption to production.
From its first week, the Blue Ocean Filter helped combat the effects of Oslo’s rising water prices by recycling wash water, and reusing the energy in the filtrate gave reduced energy costs. All as expected. Extra - and exciting - results came from the optimisation by Jako and Nor Tekstil’s engineers, building on what the Blue Ocean Filter does. The filtrate produced and then stored by the Blue Ocean Filter remains more or less at perfect wash temperature, it also still contains exactly the right amount of active oxygen and pH levels for perfect wash results for Vidar Vask’s textile mix. This allowed the washing duration to be shortened. Chemistry needs were also reduced, an environmental bonus. Whiteness checks by an external company confirmed that whiteness levels remained perfectly stable, an imperative for Vidar Vask’s high end customers.
The virtuous circle of recycling wash water and optimising the wash process produced results that impress.
The Figures
In August 2023, Jako undertook a comprehensive analysis of the Blue Ocean Filter’s performance in the period Jan-July 2023 compared to the same period in 2022, so before installation. The following emerged:
The Blue Ocean Filter effectively managed wash water streams from 6 washer extractors, the 1800 liter filtrate holding tank giving ample capacity.
All Vidar Vask’s laundry process water was recycled, leading to 4 million litres of fresh water saved in 2023.
All solid particles in the backflush water from the Blue Ocean Filter were collected in the AquaDrain, avoiding any blockage of laundry drains and ensuring that waste to sewer easily fell within local quality regulations.
Thanks to the Blue Ocean Filter as well as some process optimisations following its installation, Vidar Vask reduced its water consumption per kilo textile by 37% in the period considered, as projected.
And there was more….
Payback time on the project, projected at around 3 years, fell to just 0.8 years, a result of both the optimisations and rising water prices in Oslo.
Sensibly generous dimensioning (shout-out to Jako!) was put to good use as laundry production volumes rose through the year (by 24%).
Despite increased volumes, operational stresses reduced, as the whole project contributed to a smoother flow of work, including 33% shorter wash times.
The smoother workflow meant instead of the usual 2 or 2.5 shifts in the summer high season, Vidar Vask comfortably did their work in only 1 shift.
Rewash was cut by about 75%.
The project helped permanently reduce energy usage across the entire laundry to around 1.6kWh/Kg.
Our Takeaway
Recycling has not only saved water and energy and some expensive chemistry, but has enabled far-reaching optimisation of the Vidar Vask wash process, building on the ideal recycling and re-use loop of heated water that is exactly right for washing.
Jako assists Vidar Vask on an ongoing basis by using the Wientjens Cloud Dashboards to remotely monitor Blue Ocean Filter performance. In real life this translates to a quick daily remote equipment check by Jako, with engineers dispatched around every 2 months for routine cleaning and maintenance of the Blue Ocean Filter.
The Vidar Vask laundry operates at high efficiency and with a low costs wash process, low rewash levels, an eye to sustainability and a relaxed vibe on the workfloor because everything is simply running like clockwork. Nor Tekstil really showcases how to reap the very many benefits of recycling laundry wash water and energy.
At Wientjens, we take pride in being part of Nor Tekstil’s continuing story of excellence.
Recycling has not only saved